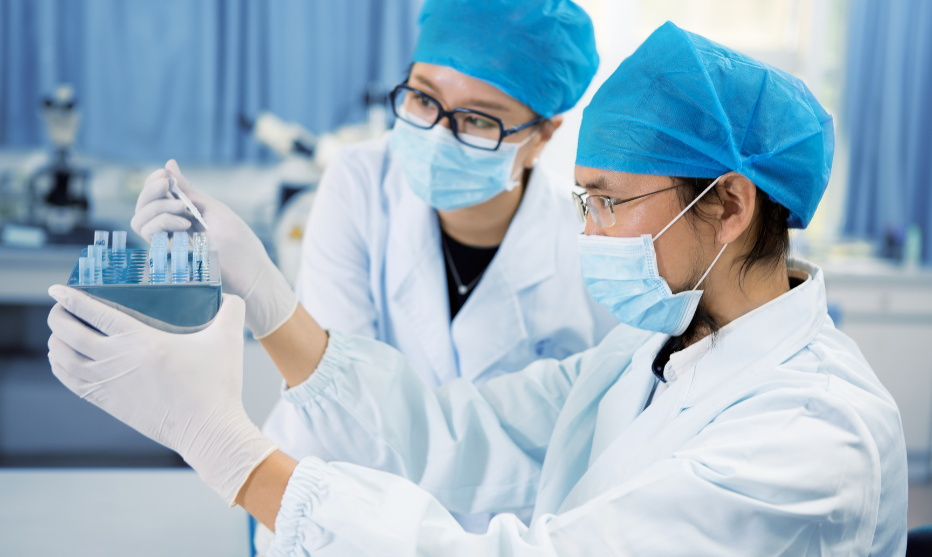
CAPA and QMS for Quality and Safety
CAPA (Corrective and Preventive Action) is a process used in QMS (Quality Management Systems).to identify and rectify the root causes of non-conformance. The goal of CAPA is not only help organizations to improve processes and avoid costly mistakes but also to protect.customers and end-users by ensuring that products and services meet safety and quality.standards (ISO 9001, LEAN Six Sigma, 21 CFR Part 820, etc.) complies with regulatory requirements.
Deviation and CAPA Management in Regulated Industries
Deviation and CAPA management are essential components of a QMS, particularly in regulated industries such as pharmaceuticals, biotechnology, and medical devices. In these industries, deviations from established procedures and standards can have significant consequences, including decreased product quality, increased risks to patient safety, and regulatory penalties.
Types of CAPA Actions
A deviation refers to any non-conformance or departure from established procedures, standards, or specifications. Deviations can occur in many different areas of a QMS, such as manufacturing processes, laboratory testing, or documentation. CAPA actions can be broadly categorized into two types:
- Corrections/Corrective Actions: These are actions taken to address the root cause of a non-conformance or problem and rectify its immediate effects. Examples of corrective actions include:
- Replacing faulty equipment;
- Updating operating procedures to correct a process issue;
- Conduct additional training for employees who were not following established procedures.
- Preventive Actions: These.are actions.taken.to prevent the reoccurrence of a non-conformance or problem in the future. Examples of preventive actions include:
- Installing additional monitoring systems to detect future issues early on;
- Process automation by reducing manual work;
- Modifying designs or specifications to eliminate potential sources of failure;
- Implementing a more robust process to reduce the chance of similar problems occurring again.
Encouraging Employees to Report Deviations
It is important to note that CAPA actions should be based on data and systematic analysis, and not simply on intuition or guesswork. This.will.ensure that the root cause of the problem is.properly addressed and that the likelihood of recurrence is minimized. Effective CAPA requires a systematic approach, including:
- Documentation.
- Analysis of non-conformances/problem identification. The one of first steps in a successful CAPA process is the identification of a non-conformance or problem. This can.be.done through various means, including internal audits, customer complaints, or monitoring of adverse events.
- Root cause analysis. Once a problem.has.been.identified, it is important to determine the root cause of the issue. This involves systematic analysis, such as the use of tools such as fishbone diagrams, the 5 whys method, or cause-and-effect.matrices, to identify the underlying factors that contributed to the problem.
- Based on the results of the root cause analysis, appropriate corrective and preventive actions should be developed and implemented to address the root cause of the problem and prevent its recurrence.
- Implementation of CAPA and its effectiveness. The effectiveness of the corrective and preventive actions.should be.monitored and documented to ensure that they.have been.successfully implemented and that the problem.has been.resolved.
- Continuous improvement/Trend Analysis: A successful CAPA process should be part of an ongoing continuous improvement program, where lessons learned from past CAPA actions are used to improve processes and prevent similar issues from occurring in the future.
Taking Action to Reported Deviations
Therefore, timely reporting of deviations and CAPA process initiation is an important part of a quality culture. Quality culture refers to the values, behaviors, and attitudes that an organization adopts to ensure that its products and services consistently meet or exceed customer expectations. Motivating employees to report deviations is essential to maintaining a strong quality culture. Here are some ways to encourage employees to report deviations:
- Create a culture of safety. Develop a culture where safety is a top priority, and employees feel safe to report any deviations or safety concerns without fear of retaliation or negative consequences.
- Establish open communication channels where employees feel comfortable reporting deviations without fear of retribution. Make it clear that reporting deviations is essential to continuous improvement and that it is a valued contribution to the organization.
- Training employees on the importance of reporting deviations, the reporting process, and the benefits of reporting. Training can also include the consequences of not reporting deviations and how they can impact the quality of products or services.
- Recognize and reward employees who report deviations. Acknowledge the contribution of the employee and the impact it had on preventing potential quality issues. This recognition can be in the form of a thank you note or a mention in a company-wide newsletter.
- Empower employees to take ownership of the process and encourage them to suggest improvements. Allow employees to make decisions and act on deviations if they have the knowledge and skills to do so.
- Continuous Improvement. Establish a culture of continuous improvement where the focus is on identifying and addressing deviations to improve quality.
- Taking action on reported deviations: Ensure that reported deviations are taken seriously and that appropriate actions are taken to address them. This will help employees feel that their reports are valued and that their concerns are being addressed.
Conclusion
Deviation and CAPA management are critical components of a quality management system, particularly in regulated industries. When an organization promotes transparency and continuous improvement, it helps to identify deviations on time and implement effective CAPA processes. This approach also ensures the quality and safety of their products, minimizes regulatory penalties risk, and maintains the trust of their customers and stakeholders.
If you have any questions don’t hesitate to contact us.